What is Scrubber
A scrubber, in a general sense, is a device or system designed to cleanse or remove unwanted substances, pollutants, or contaminants from a gas, liquid, or air stream. It’s used to improve the quality of the treated medium by eliminating harmful elements. Scrubbers find applications in various industries and environmental settings to reduce pollution, ensure compliance with regulations, and enhance overall safety and cleanliness. The term “scrubber” can refer to different technologies and methods depending on the context in which it’s used.

components of scrubber
A scrubber, particularly in an industrial air pollution control context, consists of several key components that work together to remove pollutants and contaminants from gas streams. The specific components can vary depending on the type of scrubber technology used, but here are the fundamental components you might find in a typical wet scrubber system:
- Inlet Duct: This is the point where the contaminated gas enters the scrubber system. The inlet duct directs the gas flow into the scrubber unit.
- Absorption Tower or Chamber: This is the main body of the scrubber where the actual pollutant removal takes place. It contains the scrubbing medium, which can be water or a chemical solution, depending on the pollutants being targeted.
- Spray Nozzles: These are used to introduce the scrubbing liquid (often water) into the absorption chamber in the form of fine droplets. These droplets come into contact with the contaminated gas, promoting absorption of pollutants.
- Packing Material or Tray: In some scrubbers, there might be structured packing material or trays inside the absorption chamber. These increase the contact surface area between the gas and the scrubbing liquid, enhancing pollutant absorption.
- Mist Eliminator or Demister: After the gas has passed through the absorption chamber, it might carry small liquid droplets with it. A mist eliminator is used to capture and remove these droplets, ensuring that only cleaned gas exits the scrubber.
- Outlet Duct: This is where the cleaned gas exits the scrubber system and is released into the environment or further processing.
- Pump: In systems that use a liquid scrubbing medium, a pump is used to circulate the scrubbing solution from the bottom of the absorption chamber to the spray nozzles at the top.
- Blower or Fan: Depending on the system design, a blower or fan might be used to help move the gas through the scrubber unit and ensure proper gas-liquid contact.
- Monitoring and Control Instruments: These include sensors, gauges, and controllers that measure parameters like gas flow rate, pressure, temperature, pH levels, and pollutant concentrations. This data helps optimize the scrubber’s performance and ensure compliance with regulatory standards.
- Recirculation System: In some scrubbers, a recirculation loop might be present to enhance pollutant absorption. This involves circulating a portion of the scrubbed liquid back into the absorption chamber.
- Drain System: As pollutants are absorbed by the scrubbing liquid, a drain system is used to remove the liquid containing the pollutants from the bottom of the absorption chamber for further treatment or disposal.
The exact components and their arrangement can vary based on the type of scrubber technology being used, such as wet scrubbers, dry scrubbers, or specific variations like venturi scrubbers or packed bed scrubbers.

How does scrubber works
A scrubber works by using various mechanisms to remove pollutants and contaminants from gas streams. The exact working principle can vary depending on the type of scrubber being used (wet, dry, electrostatic, etc.), but here’s a general overview of how a wet scrubber, one of the most common types, works:
Wet Scrubber Working Principle:
- Gas Entry: The gas stream containing pollutants enters the scrubber through an inlet duct or chamber.
- Contact/Reaction Chamber: In this chamber, the gas stream comes into contact with a scrubbing liquid (usually water or a chemical solution). The scrubbing liquid can be sprayed, cascaded, or allowed to flow over surfaces, creating a large contact area between the gas and the liquid.
- Particle Capture: As the gas passes through the scrubbing liquid, various mechanisms come into play to capture pollutants:
- Impaction: Larger particles are captured when they collide with droplets of the scrubbing liquid.
- Adsorption: Gaseous pollutants may be absorbed into the liquid through physical or chemical processes.
- Chemical Reactions: Some pollutants react chemically with the scrubbing liquid, forming compounds that can be collected.
4.Droplet Formation: The scrubbing liquid breaks into small droplets, increasing the surface area available for gas-liquid interaction. This maximizes the chances of pollutants being captured.
5.Packing Material (if applicable): In scrubbers that use packing material, such as packed bed scrubbers, the gas passes through a structured arrangement of materials. This increases the surface area even further, enhancing pollutant capture.
6.Mist Elimination: After the gas passes through the contact chamber, it might still carry small liquid droplets. A mist eliminator or demister removes these droplets from the gas stream, preventing liquid carryover.
7.Cleaned Gas Exit: The gas stream, now stripped of a significant portion of its pollutants, exits the scrubber through an outlet duct or stack.
8.Slurry or Liquid Collection (if applicable): In some cases, a scrubber generates a liquid slurry containing captured pollutants. This slurry needs to be collected, treated, and disposed of properly according to environmental regulations.
9.Controls and Monitoring: Modern scrubber systems often include controls and monitoring devices that adjust the flow rates of gas and liquid, maintain optimal pH levels, and ensure efficient operation.
The specific working mechanisms might differ based on the type of pollutants, scrubbing liquid, and design of the scrubber. The ultimate goal of a scrubber is to effectively remove pollutants from gas streams, reducing emissions and contributing to improved air quality and environmental compliance.
types of scrubber
There are several types of scrubbers used in various industries to remove pollutants and contaminants from gas streams. Each type of scrubber is designed to address specific types of pollutants and operating conditions. Here are some common types of scrubbers:
1. Wet Scrubbers:
- Venturi Scrubbers: These scrubbers create a constriction in the gas stream, causing turbulence and enabling the mixing of pollutants with a scrubbing liquid. The turbulence helps capture particles and gases.
- Packed Bed Scrubbers: These scrubbers use a packed bed of materials like structured packing or random packing to increase the contact surface area between the gas and the scrubbing liquid, enhancing pollutant absorption.
- Spray Tower Scrubbers: In these scrubbers, the gas stream passes through a chamber where the scrubbing liquid is sprayed from nozzles. The liquid droplets capture pollutants as they come into contact with the gas.
- Bubble Cap Tray Scrubbers: Similar to spray tower scrubbers, but instead of sprays, gas passes through bubble cap trays where scrubbing liquid flows over the trays and creates bubbles that capture pollutants.
- Impingement Plate Scrubbers: Gas and liquid are forced to collide on impingement plates, promoting the capture of particles through impaction and subsequent liquid droplet collection.
2. Dry Scrubbers:
- Dry Sorbent Injection (DSI) Systems: Dry sorbents like lime or sodium bicarbonate are injected into the gas stream, reacting with acidic gases to form solid byproducts that can be collected.
- Spray Dry Scrubbers: These scrubbers use a dry sorbent sprayed into the gas stream as fine droplets. The gas-solid reactions occur as the droplets dry, capturing pollutants.
- Fluidized Bed Scrubbers: In fluidized bed scrubbers, dry sorbents are suspended in an upward-flowing gas stream. Pollutants react with the sorbent particles as they circulate in the fluidized bed.
3. Electrostatic Precipitators (ESPs):
- While not traditional wet or dry scrubbers, ESPs are electrostatic devices that use an electric field to charge and collect particulate matter and aerosols from gas streams.
4. Gas Absorption Scrubbers:
- Ammonia Scrubbers: These scrubbers use a scrubbing solution to absorb and neutralize ammonia gas from industrial processes.
- Hydrogen Sulfide Scrubbers: Scrubbers designed to remove hydrogen sulfide gas from gas streams, often used in wastewater treatment and biogas facilities.
5. Selective Catalytic Reduction (SCR):
- SCR systems use catalysts to facilitate chemical reactions that convert nitrogen oxides (NOx) into nitrogen gas and water vapor, reducing NOx emissions.
6. Activated Carbon Adsorption:
- Activated carbon scrubbers use adsorption to capture volatile organic compounds (VOCs) and other pollutants from gas streams.
The choice of scrubber type depends on factors such as the specific pollutants to be removed, gas flow rates, temperature, humidity, and regulatory requirements. Industries select the most suitable scrubber technology to effectively and efficiently meet their emission control needs.

application of Scrubber
Scrubbers have diverse applications across various industries and environmental contexts. Some of the key applications of scrubbers include:
- Industrial Emission Control: Scrubbers are extensively used in industries such as power generation, manufacturing, and chemical production to remove harmful gases like sulfur dioxide (SO2), nitrogen oxides (NOx), hydrogen chloride (HCl), and particulate matter from exhaust gases before they are released into the atmosphere.
- Air Quality Improvement: Scrubbers play a vital role in improving the air quality of urban and industrial areas by reducing emissions of pollutants that contribute to smog, acid rain, and respiratory illnesses.
- Wastewater Treatment: In water treatment facilities, scrubbers are employed to remove contaminants from wastewater and industrial effluents, ensuring that harmful substances do not contaminate natural water bodies.
- Marine Industry: Marine scrubbers, often referred to as exhaust gas cleaning systems (EGCS), are used in ships to remove sulfur oxides from the exhaust gases of marine engines, helping vessels comply with international emission standards.
- Mining Operations: Scrubbers are used to control dust emissions in mining and mineral processing operations, preventing the dispersion of harmful particles into the surrounding environment.
- Chemical Processing: Scrubbers are employed in chemical plants to neutralize or remove hazardous fumes and byproducts produced during various chemical reactions.
- Oil and Gas Industry: In oil refineries and natural gas processing plants, scrubbers help remove sulfur compounds and other pollutants from process gases to meet regulatory requirements.
- Food Processing: Scrubbers can be used in food processing facilities to control odors and remove airborne contaminants from cooking or production processes.
- Laboratories and Cleanrooms: Scrubbers help maintain sterile and controlled environments in laboratories, cleanrooms, and medical facilities by filtering out airborne particles and contaminants.
- Agricultural Operations: Scrubbers can be used in agricultural settings to mitigate odors and gases produced by livestock operations and waste management facilities.
- Nuclear Industry: Scrubbers are used in nuclear power plants to remove radioactive particles from the air, enhancing safety and preventing the release of radioactive substances.
- Electronics Manufacturing: In semiconductor manufacturing and electronics assembly, scrubbers help control airborne contaminants and maintain clean conditions essential for production processes.
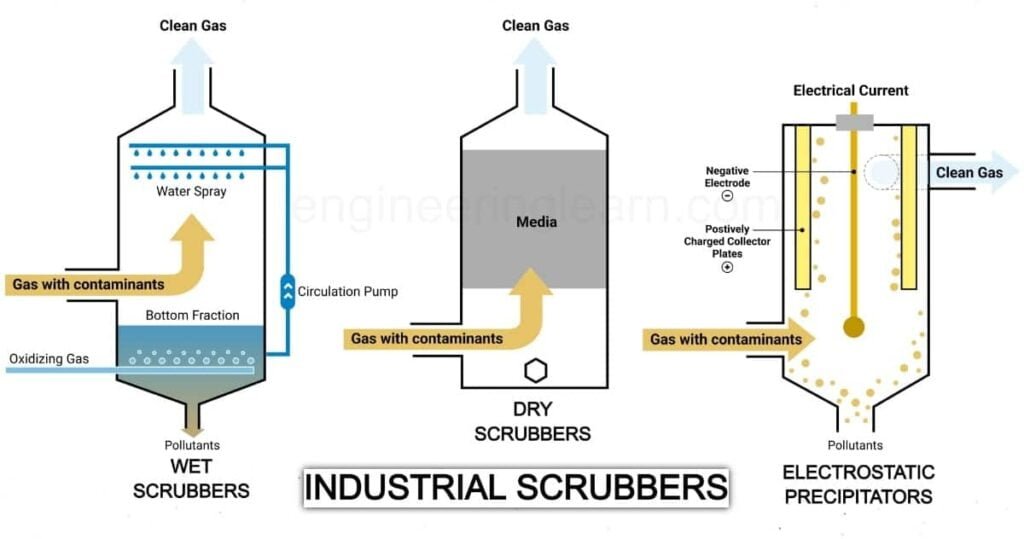
The specific type of scrubber and its design depend on the application and the pollutants or contaminants that need to be removed. Scrubbers play a crucial role in reducing environmental impacts, improving health and safety, and ensuring compliance with regulations across a wide range of industries.
Advantages of Scrubber
Scrubbers offer several advantages in a variety of industrial and environmental settings. Some of the key advantages of using scrubbers include:
- Pollution Control: Scrubbers are highly effective in removing pollutants and contaminants from exhaust gases, liquids, and air streams. They contribute to reducing emissions of harmful substances, thereby mitigating air and water pollution.
- Compliance with Regulations: Industries are often subject to strict environmental regulations and emissions standards. Scrubbers enable companies to meet these requirements by significantly reducing emissions of pollutants, helping avoid penalties and legal issues.
- Improved Air Quality: By removing harmful gases and particulate matter from industrial exhausts, scrubbers play a crucial role in improving overall air quality. This is essential for protecting human health and the environment.
- Health and Safety: Scrubbers enhance workplace safety by reducing exposure to toxic fumes, hazardous gases, and airborne particulates. This is especially important in industries where employees are at risk of exposure to harmful substances.
- Preventing Acid Rain: Scrubbers that remove sulfur dioxide (SO2) and nitrogen oxides (NOx) from exhaust gases help prevent the formation of acid rain, which can damage ecosystems, soil, water bodies, and infrastructure.
- Odor Control: In various industries, scrubbers are used to eliminate foul odors generated during manufacturing processes, wastewater treatment, and other operations. This helps create a more pleasant environment for workers and nearby communities.
- Reduced Corrosion: Scrubbers can reduce the presence of corrosive gases in industrial exhaust, which helps extend the lifespan of equipment and infrastructure, leading to cost savings.
- Energy Recovery: Some scrubber designs allow for the recovery of energy or valuable chemicals from the captured pollutants, turning a potential waste stream into a resource.
- Versatility: Scrubbers can be designed to handle a wide range of pollutants, making them versatile solutions for various industries and applications.
- Public Relations and Reputation: Implementing effective pollution control measures, such as using scrubbers, demonstrates a company’s commitment to environmental responsibility, which can enhance its reputation among stakeholders and the public.
- Global Environmental Impact: Widespread use of scrubbers contributes to global efforts to mitigate climate change and reduce the release of greenhouse gases and other pollutants into the atmosphere.
- Customization: Scrubbers can be tailored to suit specific industrial processes and pollution control needs, ensuring optimal performance.
While scrubbers offer numerous advantages, their implementation should be carefully planned to ensure proper design, operation, and maintenance. This ensures that the desired benefits are achieved without any unintended negative consequences.

Disadvantages of Scrubber
While scrubbers offer numerous benefits, they also come with certain disadvantages and challenges that should be considered. Some of the disadvantages of scrubbers include:
- Initial Cost: The installation of scrubber systems can involve significant upfront costs, including equipment purchase, engineering, installation, and integration with existing processes. This cost factor can be a deterrent for some industries, especially smaller businesses.
- Maintenance and Operating Costs: Scrubber systems require regular maintenance, monitoring, and operational costs. This includes expenses for replacing scrubber media, cleaning components, and addressing potential technical issues.
- Energy Consumption: Certain types of scrubbers can consume a notable amount of energy to operate efficiently, potentially offsetting the environmental benefits gained from pollutant removal.
- Complexity: The design, installation, and operation of scrubber systems can be complex, requiring specialized knowledge and skilled personnel to ensure optimal performance.
- Space Requirements: Scrubbers may require dedicated physical space within an industrial facility, which can be challenging to accommodate, particularly in crowded or confined settings.
- Waste Management: Scrubber systems generate waste products, such as captured pollutants or spent scrubbing solutions, which must be properly managed and disposed of according to regulations.
- Chemical Usage: Some scrubber systems require the use of chemicals or reagents to facilitate pollutant removal. The handling, storage, and disposal of these chemicals can introduce additional complexities and environmental considerations.
- Byproduct Generation: While some scrubbers may recover valuable byproducts, others may generate waste streams that need proper treatment, potentially leading to additional costs and environmental concerns.
- Efficiency Trade-offs: Depending on the design and operation, certain scrubber systems might have trade-offs in terms of pollutant removal efficiency versus energy consumption or cost-effectiveness.
- Limited Effectiveness for Certain Pollutants: Scrubbers might not be equally effective at removing all types of pollutants. Some gaseous compounds, such as volatile organic compounds (VOCs), might require specialized scrubber technologies for effective removal.
- Environmental Impact: The production, maintenance, and disposal of scrubber components can have their own environmental impact, potentially offsetting some of the benefits gained from pollutant removal.
- Transition Period: Retrofitting existing industrial processes with scrubbers might require temporary shutdowns or adjustments, impacting production and operations during the transition.
- Water Usage: Wet scrubbers, which rely on water for pollutant capture, can have water usage implications in regions where water resources are scarce.
- Maintenance Downtime: Scheduled maintenance and occasional unexpected downtimes for maintenance or repairs can disrupt industrial operations.
- Specific Applications: Some industries or processes might have unique challenges that make the implementation of scrubbers less practical or effective for certain pollutants.
When considering the implementation of scrubbers, it’s important to weigh these disadvantages against the benefits and conduct a thorough cost-benefit analysis tailored to the specific industry and context.
Check Out Other Important Topics
IC Engine | Important PDFs | Boilers | Synergy Maritime Exam | Naval Arch | MEO Class 4 |
Interview Questions | Difference Between | Types of Pumps | Auxiliary Machines | Types of Valves | Home |