Fuel oil system in ship For marine diesel engine are which operate on heavy fuel oils: Fuel oil transfer system, Fuel oil treatment system and Fuel oil supply system.Various piping systems for bunkering, storage, transfer, offloading, and treatment of fuel oils are provided.
Fuel Oil Transfer System
This system receives, stores, and delivers fuel to settling tanks. Fuel oils are loaded through deck fill ( bunker manifold ) connections with sample connections to allow the fuel to be sampled as it is brought aboard. HFO is stored in tanks equipped with heating coils.
HFO is transferred to the fuel oil settling tanks via FO transfer pumps equipped with a suction strainer in preparation for use. The piping is set up so that the pumps can transfer fuel from storage tanks to deck connections for offloading. Settling tanks are used to allow gross water and solids to settle to the bottom of the tank.
Fuel Oil Treatment System
Fuel oil is transferred from the settling tanks to the service tanks via the FO treatment system. The two-stage process is commonly used for cleaning heavy fuel oils (HFO). The fuel is heated to about 50-60°C in a settling tank before being drawn out by the purifier inlet pump.
The fuel is delivered by the inlet pump to a thermostatically controlled heater, which raises the fuel temperature to approximately 80°C, and then to the centrifugal purifier. The purifier discharge pump then transfers the dry purified fuel to a centrifugal clarifier. Following clarification, the clarifier discharge pump transports the fuel to the service tank for use by the engine.
Fuel Oil Supply System
The fuel from the service tank is delivered to the diesel engine via this system.
This system consist of :-
1.Fuel oil storage tank (heavy fuel oil )
2.Transfer pump
3.settling tank
4.Circulating pump on separator
5.Preheater
6.Seperator
7.Tank for purified oil
8.Shut off valves
9.Tank for purified diesel oil
10.Shut off valve
11.3-way valve
12.Flow meter
13.Mixing tank
14.Vapour trap
15.Booster pump
16.preheater
17.Filter, heatable
18.Thermometer
19.Fuel pump feed pipe
20.Fuel injection pump
21.High – pressure fuel pipe
22.Fuel injector
23.Diesel Engine
24.Fuel return pipe
25.Pressure Gaye
26.Constant Pressure Valve
27.Prewarming by -pass
Fuel oil supply for a two-stroke diesel engine
A slow-speed two-stroke diesel engine is usually configured to run continuously on heavy fuel and to have a diesel oil supply available for maneuvering purposes.
The oil in the system shown in Figure is stored in tanks with a double bottom, from which it is pumped to a settling tank and heated. After passing through centrifuges, the cleaned, heated oil is pumped to a daily service tank.

To ensure constant supply of fuel to the mixing tank via the fuel oil pipes and the flowmeter,the heavy fuel oil tank should be located high enough over the mixing tank.To rule out the possibility of heavy fuel oil entering the diesel oil day tank ,the latter should be located above the heavy fuel oil tank or protected by means of a non return valve.
The oil flows from the daily service tank to a mixing tank via a three-way valve. A flow meter is installed in the system to monitor fuel consumption. Booster pumps are used to deliver oil to engine-driven fuel pumps after passing it through heaters and a viscosity regulator. The fuel pumps will deliver high-pressure fuel to the injectors.
The viscosity regulator regulates the temperature of the fuel oil in order to provide the proper viscosity for combustion. A pressure regulating valve ensures that the engine-driven pumps have a constant supply of pressure, and a pre-warming bypass is used to warm up the fuel before starting the engine.
A diesel oil daily service tank that is connected to the system via a three-way valve can be installed. The engine can be started and maneuvered using diesel oil or a combination of diesel and heavy fuel oil. The mixing tank collects recirculated oil and also serves as a buffer or reserve tank, supplying fuel when the daily service tank is empty.
In the event of problems during manoeuvring on heavy oil engines, there should be no hesitation in switching to diesel oil, regardless of whether the engines are operated via bridge control or engine room control.
Main engines designed to run on heavy fuel oil must be used in accordance with the manufacturer’s instructions. All other types of main engines must be operated on diesel oil in accordance with the manufacturer’s instructions.
Safety services fitted on fuel system on ship
The system includes several safety devices, including low-level alarms and remotely operated tank outlet valves that can be closed in the event of a fire
1.Quick closing valves on settling/service tanks
2.relief valves on 2 pumps/heaters
3.quick closing valve on mixing/vent tank
4.pipes lagged/save-alls under pumps and heaters
5.low fuel oil pressure alarm
6.high fuel oil pressure alarm
7.low fuel oil temperature alarm
8.high fuel oil temperature alarm
9.emergency remote stops for pumps
10.high pressure pipes between fuel injection pump and injector are double skinned.
Of Each Components of fuel oil system of ship
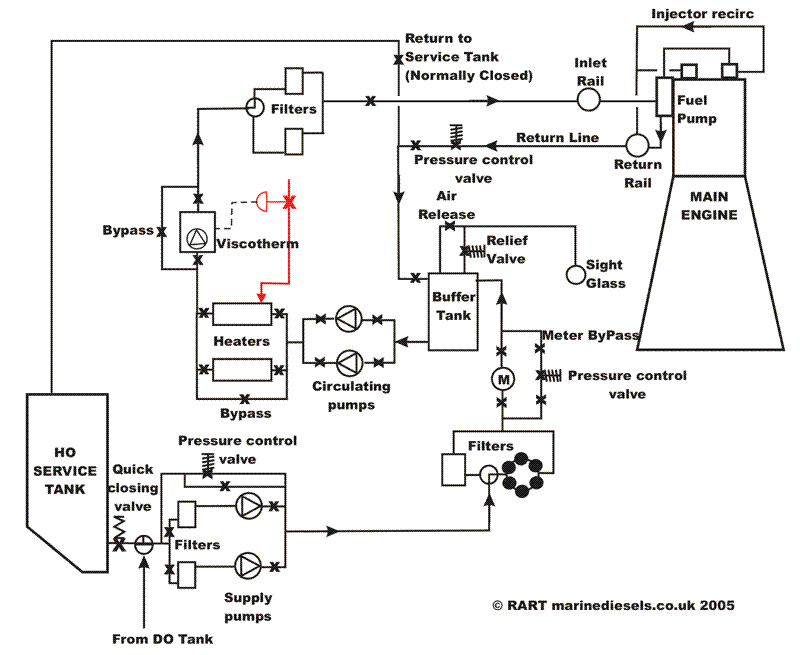
1.Service tank :-Fuel is transferred to the service rank via a centrifuge from service tank.
2.Change over switch :- The switch in the engine control room or the handwheel on top of the valve can be used to operate the change over valve automatically.
It used to be common practice to switch to diesel fuel for maneuvering purposes. Modern methods of fuel oil recirculation to keep the fuel hot at the injectors have rendered this practice obsolete.
3.Quick closing valve :- Fuel is drawn from service tank through a quick closing valve. These can be closed remotely in case of emergency (e.g. fire). This can be done with simple pull wires, hydraulically, or by compressed air.
The fuel then passes via the change over valve through a set of filters into the supply pumps.
4.Filter :-A suction filter removes any particles that could cause damage before the fuel enters the supply pumps. There are two filters, one for each of the two pumps. They are made of fine metal gauze and can be cleaned and reused as needed.
5.Pump :- The pressure is raised to about 7 bar by the supply pumps. A pressure regulating valve is used to keep the discharge pressure constant.
6.Regulating valve :-There is also a manual bypass which can be used should the regulating valve develop a fault.
7.Auto back filter :-The fuel is passed from the supply pumps to a series of backflushing filters (25 micron). The filter elements are housed in the pods. When the filters begin to clog, a differential pressure sensor triggers a backflushing routine, which allows the filters to clean themselves. Backflushing oil containing sediment from the filters drains to the fuel oil drain tank, where it can be recovered and purified.
When a mesh type filter is used, the filter can be removed from service line for cleaning.
8.Flowmeter :-
The fuel is pumped via a meter so that the quantity of fuel used can be monitored and the specific fuel consumption of the engine calculated.
In the case that the meter has to be bypassed, then the fuel is led across a pressure retaining valve.
9.Mixing column :- The fuel is then passes to a mixing column or buffer tank where it mixes with returned fuel from the main engine.
The mixing column is fitted with a relief valve and an air release (see in the fig ) and the outlets from these are led via a sight glass to the fuel oil drain tank.
10.Booster pump :- Fuel oil circulating pumps from the buffer tank pressurize the fuel to about 8 bar before it is passed to the heaters and engine.
11.Steam is used to heat the oil (although thermal oil or electric heaters are used on other systems). A viscosity measuring device regulates the temperature of the oil. The viscosity must be kept at the proper level for injection. It is set to 16 centistokes on this particular system.
12.Filter :-
After passing through the heater and before reaching the main engine inlet rail, the fuel is filtered once more to ensure that it is free of abrasive contaminants that could damage the fuel pumps, injectors, and cylinder liner.
13.Fuel oil inlet rail :-
Fuel enters each fuel pump from the main engine inlet rail (one per cylinder). The fuel pump delivers high-pressure fuel (250bar or higher) to the fuel injector (s).
14.The fuel return is the lower connection on the fuel pump. More fuel than is required is delivered to the pump. The surplus is returned to the buffer (mixing) tank.
The atomized fuel is delivered to the cylinder by the fuel injectors. When no fuel is being injected, the injectors recirculate back to the fuel return.
14.Back pressure control valve :- A backpressure control valve is installed on the return line to keep the fuel oil pressure at the required level (on this system, about 8 bar).
Check Out Other Important Topics
Home IC Engine Electrical Important PDFs Boilers Synergy Maritime Exam Naval Arch Interview Questions Difference Between Types of Pumps Types of Valves MEO Class 4 Auxiliary Machines